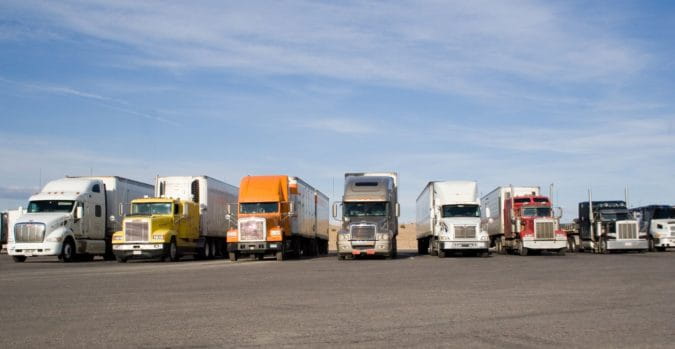
'Tis the holiday shopping season and consumers are no longer waiting in long lines for the hot new holiday gift items, preferring to instead fulfill their wish list through just a few clicks. This holiday season, customers will expect their purchases to be on their doorstep in no time at all, at an extremely affordable cost or, ideally, free. Over the years, customers have become accustomed to low or free shipping costs from many large retailers, most notably Amazon, and even their favorite small boutiques. Free shipping is now the customer expectation, but how did we get here?
Amazon has been the leader in the industry thanks to their reinvention of an optimized supply chain, which has led to the revolutionary “Amazon Prime” two-day (or even one-day) shipping promise. Many companies have had to follow suit and adopt the “Amazon way." However, most retailers lack the proper capital and technology to address the free shipping expectation. Due to two upcoming disruptors in the industry, electronic logging devices and driver shortages, retailers will need to adapt their shipping practices to drive costs down and keep delivering on the free shipping promise.
ELDs synchronize with a carrier truck’s engine to automatically record driving time for more accurate hours-of-service (HOS) reporting. This nice-to-have technology will soon be a must for most commercial trucking operations as announced by the Federal Motor Carrier Safety Administration. The noble goal of creating a safer work environment for drivers will largely impact a shipping industry that has historically incentivized drivers to haul farther, faster, and stretch log books to outpace their competition. Tighter regulation and reporting that requires a driver to turn in for the night will cause the extension of many delivery time frames. This means deliveries ranging from 450-600 miles will be stretched from one to two days. Consumers will be waiting longer for their goods and shippers will experience slimmer margins. Reduced capacity is estimated to cause a four percent increase in contract rates and a 15 to 20 percent increase in spot pricing for hauls.
Until drones and driverless trucks become commonplace for all packages, truck drivers will continue to be the major labor force behind getting purchases from the warehouse to end consumers. The shipping industry is feeling the pinch on the available number of drivers in the workforce and projections state that by 2022, there will be a shortage of at least 160,000 drivers. Carriers, or the truck driving companies themselves, will be able to demand premium rates, specifically on lower volume shipping lanes, further squeezing the margins of retailers. Retailers may turn to freight brokers to find capacity, resulting in higher overall transportation costs.
The most successful companies have learned how to keep pace with the disruptors in their industry. Based on the experience and best practices of some of our most proactive clients, there are three potential strategies to consider in order to reduce your supply chain shipping costs and keep up with your customers’ “we want it now” mentality.
The free (and fast) shipping expectation is not going anywhere. Retailers need to increase their efficiency or change their shipping methodologies to keep costs low. This holiday season, take some time to review and safeguard your shipping strategy to ensure you can keep up with your industry disruptors and be prepared to meet customers’ expectations in the year to come.